3D Printing: Beyond the Basics
A team at MIT modified a 3D printer to produce compact and powerful solenoids that could be used to repair equipment in remote regions.
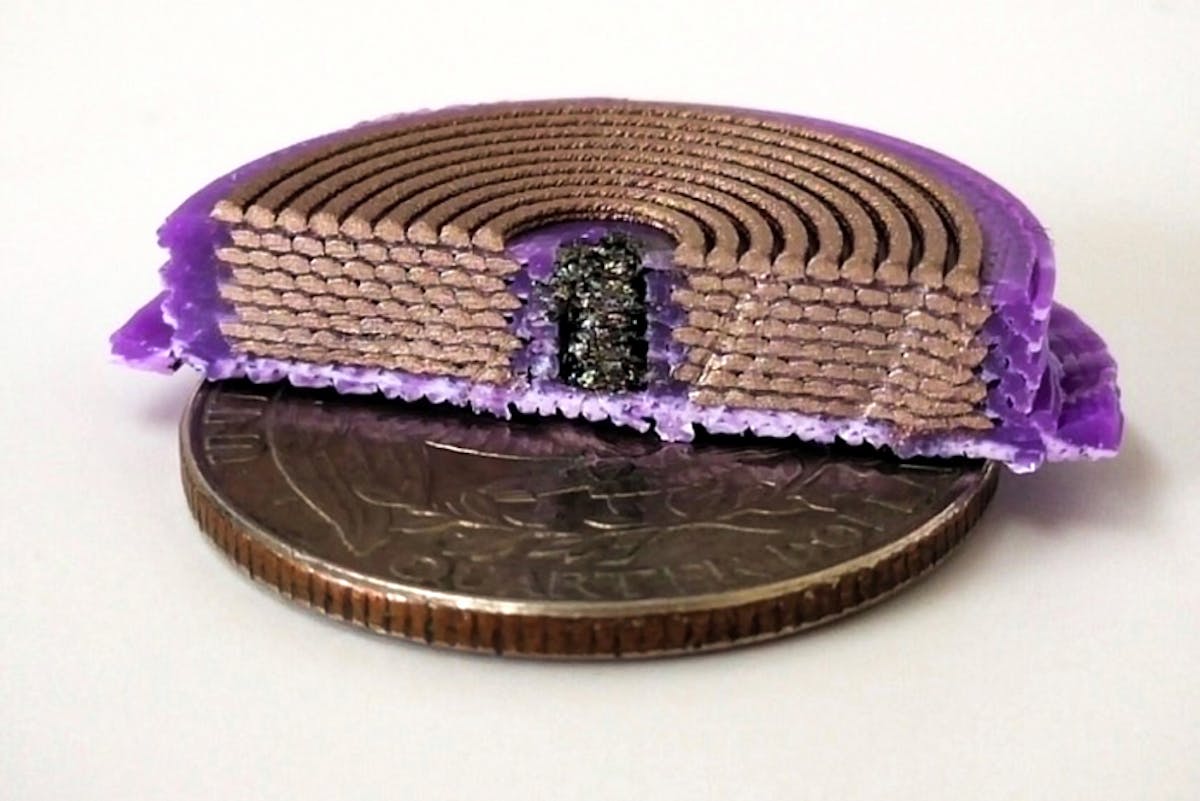
Additive manufacturing, commonly known as 3D printing, has changed the way we produce objects, enabling the creation of complex designs layer by layer directly from digital models. One of its most significant advantages is its capacity to produce parts in small quantities outside of traditional factories. This capability is transformative, particularly in remote areas or even in space, where traditional supply chains are non-existent.
As the state of the art has advanced, additive manufacturing has moved beyond the printing of just basic parts to also include simple electronic devices. This integration of electronics with 3D printing technology opens up a myriad of possibilities, from custom sensors for environmental monitoring in remote locations to on-demand production of medical devices tailored to individual patient needs. The ability to seamlessly incorporate electronic components into 3D-printed objects expands the scope of what can be achieved, pushing the boundaries of innovation and customization.
But this is still an emerging discipline within the field, and there is much work to be done before people in a remote part of the world 3D print, for example, a dialysis machine to treat kidney failure. Engineers at MIT have recently published the results of an effort to move the field forward, however. In this work, the team built a customized 3D printer and demonstrated that it could be used to produce an electronic component that is crucial in many applications — a solenoid.
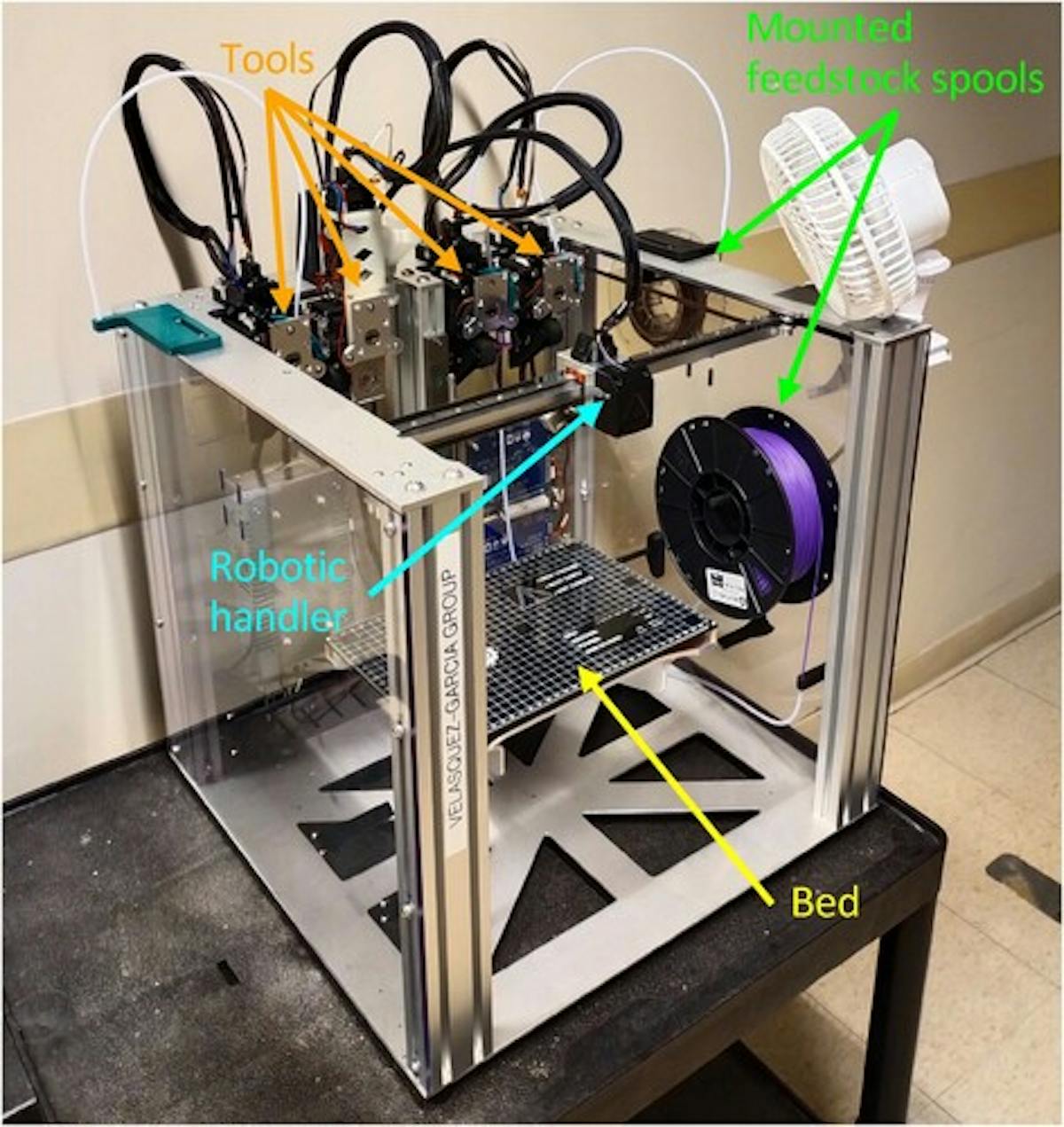
As a quick refresher, solenoids are electromechanical devices that convert electrical energy into linear mechanical motion. They are commonly used in valves, locks, relays, and more, which make them important in building, or repairing, a great many devices. They are also relatively simple, and can be constructed of as few as three materials: an insulator, a conductor, and a magnetic material. This simplicity makes them good targets for production via additive manufacturing.
Previous attempts to 3D print solenoids have produced devices that were oversized and underpowered, however, limiting their usefulness. To overcome these issues, the researchers modified an off-the-shelf multi-material extrusion 3D printer so that it could produce a more powerful and compact solenoid in a single step.
A four nozzle printer was selected — while only three materials were actually needed, this arrangement made it easier to experiment with different material options. One of the nozzles was modified so that it could extrude pellets rather than filament. This enabled them to use a magnetic nylon material that has metallic particles embedded within it. It is virtually impossible to turn this material into a filament, but it can be used to produce far better performing solenoid plungers than other available materials.
An appropriate conductive material was available as a filament, but it would frequently melt and jam the nozzle, causing the print to fail. But with some added ventilation (and a relocated spool to avoid damaging this fragile material), the problem was resolved. Including the modifications, the cost of the 3D printer came in at about $4,000, which is considerably less than competing technologies.
Using this system, the team produced a solenoid with eight layers of coiled conductive material sandwiched between an insulator. It proved to be considerably smaller than previous 3D-printed solenoids, with a diameter that is about the size of a quarter. It also proved to perform quite well — the magnetic field it produced was three times stronger than other devices.
Looking ahead, the researchers intend to experiment with additional materials to see if they can further enhance the performance. With further work, future techniques may allow us to 3D print all manner of electronic components. Imagine not having to wait for an online order to arrive to finish your weekend projects!
R&D, creativity, and building the next big thing you never knew you wanted are my specialties.