Recycle 3D Printer Filament with This Low-Cost DIY Extruder
Want to put your plastic waste to good use? Build this affordable machine to turn it into 3D printer filament.
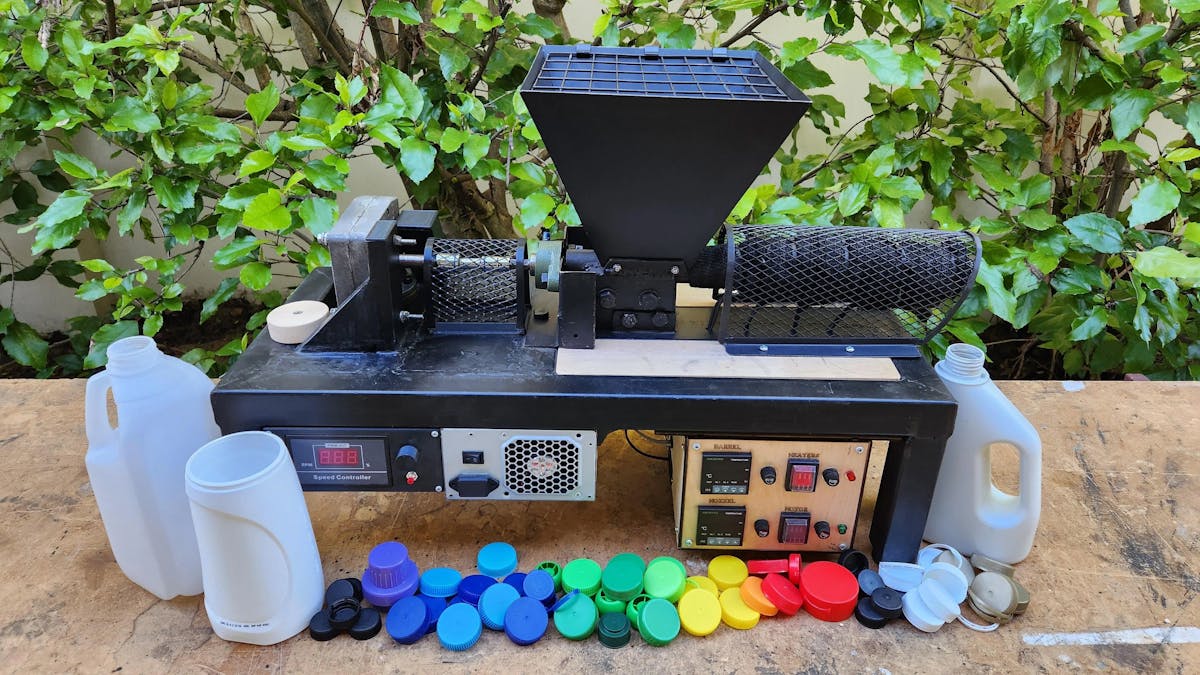
FDM (fused-deposition modeling) 3D printers use plastic. And while the resulting waste isn’t even a drop in the global bucket and pales in comparison to traditional fabrication methods, many hobbyists are eager to reduce their contribution to the problem of plastic waste. Fortunately, FDM 3D printers use filament made of thermoplastic and it is possible to reuse that — and household waste plastic — for new print jobs. To make that process affordable, Thomas (AKA Tin Foil Hat) designed this DIY extruder.
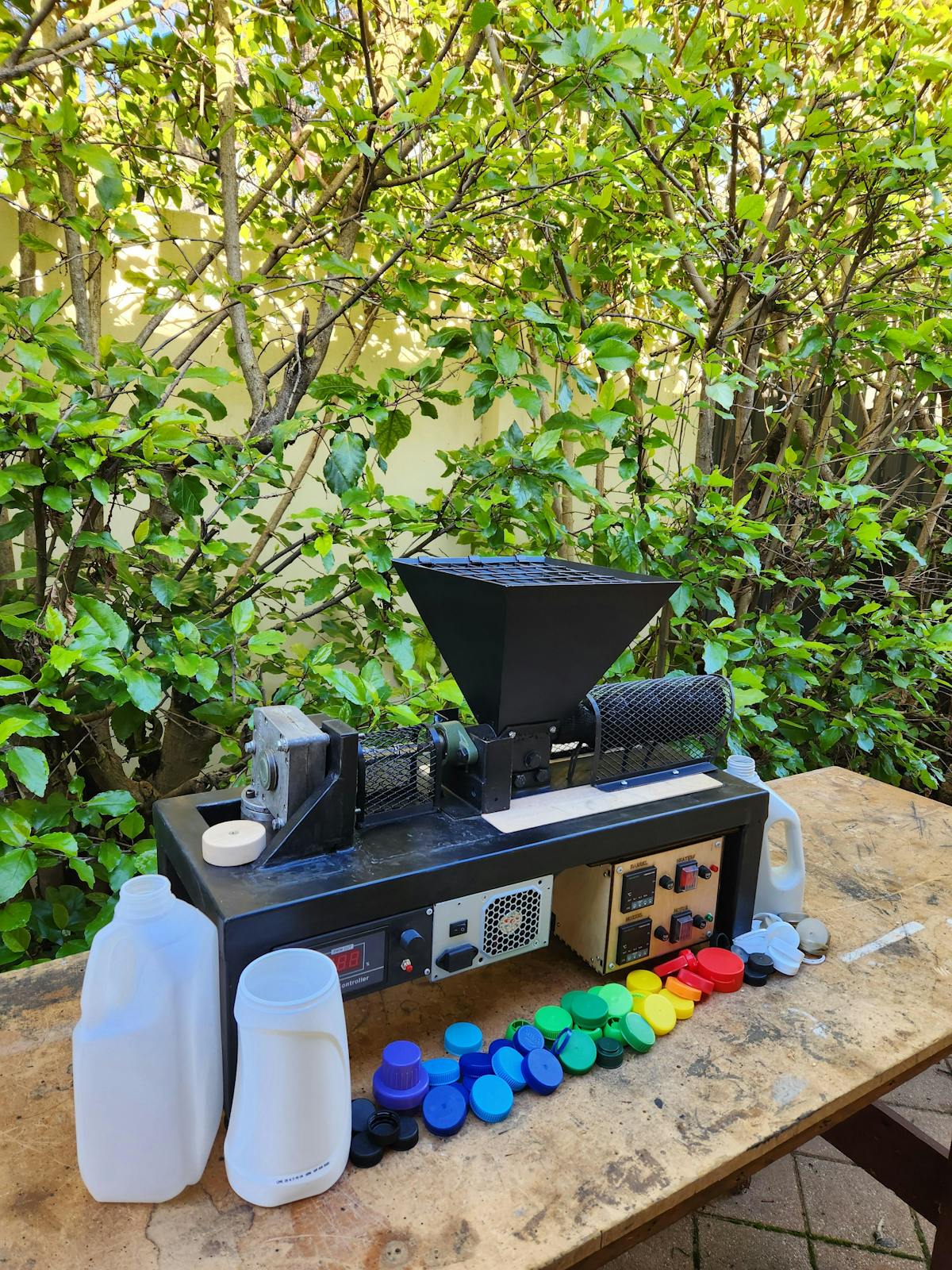
Resin 3D printers, including the MSLA (masked stereolithography) models that are popular on the consumer market, utilize photopolymer resin that undergoes a chemical change (photopolymerization) when exposed to UV light. There isn’t any way to reverse that chemical reaction, so the material in an MSLA-printed part can’t be used again.
But FDM printers are different, because they use filament made of thermoplastic. When exposed to heat, the filament melts. When it cools, it solidifies. No chemical reaction occurs, so this process is repeatable and that’s exactly why Tin Foil Hat's DIY extruder works.
The first step is to shred and grind suitable thermoplastic waste down into small fragments, done with a separate machine. That waste can come from failed prints, parts that aren’t useful anymore, or garbage. It just needs to be clean and of a similar type. Some thermoplastics are impractical for 3D printing, but there is information available online about every material you’re likely to come across. The shredded plastic feeds from a hopper into an auger that pushes into a hot end, similar to the one on your 3D printer. The extruded plastic can then be drawn through a nozzle and spooled for use in a 3D printer.
This machine works a lot like a 3D printer, but with only an “E” axis and hopper/auger instead of a conventional direct drive or Bowden extruder. It needs a motor with speed controller to drive the auger and two sets of temperature control components. The latter consist of PID temperature controllers, thermocouples, and solid-state relays. Together, they control the heaters that melt thermoplastic as it enters into the hot end, maintaining the proper temperature to ensure consistent extrusion without burning.
Those components, along with the power supply and mechanical parts, all mount onto a frame made of welded steel tube. As Tin Foil Hat points out, welding may sound intimidating to the uninitiated, but the basics of MIG welding are easy to learn.
The resulting machine will let you take advantage of thermoplastic that would likely end up in a landfill otherwise. However, it is worth noting that the filament produced by this machine will be inconsistent — both in geometry and composition. It will still work, but won’t be as good as new filament from a factory.
Writer for Hackster News. Proud husband and dog dad. Maker and serial hobbyist. Check out my YouTube channel: Serial Hobbyism